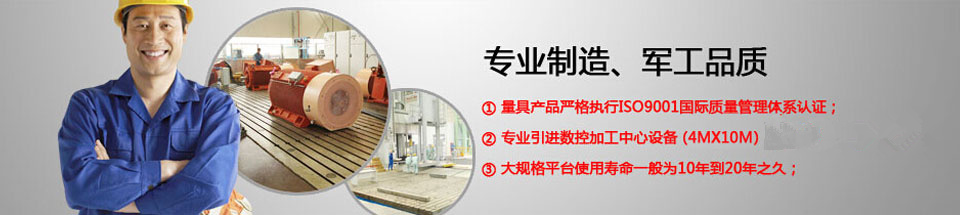
北重鑄造廠家常用鑄造方法的缺陷及控制
北重鑄造廠家常用鑄造方法的缺陷及控制:
一、鑄造的定義和分類
鑄造的定義:是將液體金屬澆鑄到與零件形狀相適應的鑄造空腔中,待其冷卻凝固后,獲得具有一定形狀、尺寸和性能金屬零件毛坯的成型方法。
常見的鑄造方法有砂型鑄造和精密鑄造,詳細的分類方法如下表所示。
砂型鑄造:砂型鑄造——在砂型中生產鑄件的鑄造方法。鋼、鐵和大多數有色合金鑄件都可用砂型鑄造方法獲得。由于砂型鑄造所用的造型材料價廉易得,鑄型制造簡便,對鑄件的單件生產、成批生產和大量生產均能適應,長期以來,一直是鑄造生產中的基本工藝。
精密鑄造:精密鑄造是用精密的造型方法獲得精確鑄件工藝的總稱。它的產品精密、復雜、接近于零件最后形狀,可不加工或很少加工就直接使用,是一種近凈形成形的先進工藝。
圖片
鑄造方法分類
二、常用的鑄造方法及其優缺點
1. 普通砂型鑄造
制造砂型的基本原材料是鑄造砂和型砂粘結劑。最常用的鑄造砂是硅質砂,硅砂的高溫性能不能滿足使用要求時則使用鋯英砂、鉻鐵礦砂、剛玉砂等特種砂。應用最廣的型砂粘結劑是粘土,也可采用各種干性油或半干性油、水溶性硅酸鹽或磷酸鹽和各種合成樹脂作型砂粘結劑。
砂型鑄造中所用的外砂型按型砂所用的粘結劑及其建立強度的方式不同分為粘土濕砂型、粘土干砂型和化學硬化砂型3種。
圖片
砂型鑄造用的是最流行和最簡單類型的鑄件已延用幾個世紀.砂型鑄造是用來制造大型部件,如灰鑄鐵,球墨鑄鐵,不銹鋼和其它類型鋼材等工序的砂型鑄造。其中主要步驟包括繪畫,模具,制芯,造型,熔化及澆注,清潔等。
工藝參數的選擇
加工余量:所謂加工余量,就是鑄件上需要切削加工的表面,應預先留出一定的加工余量,其大小取決于鑄造合金的種類、造型方法、鑄件大小及加工面在鑄型中的位置等諸多因素。
起模斜度:為了使模樣便于從鑄型中取出,垂直于分型面的立壁上所加的斜度稱為起模斜度。
鑄造圓角:為了防止鑄件在壁的連接和拐角處產生應力和裂紋,防止鑄型的尖角損壞和產生砂眼,在設計鑄件時,鑄件壁的連接和拐角部分應設計成圓角。
型芯頭:為了保證型芯在鑄型中的定位、固定和排氣,模樣和型芯都要設計出型芯頭。
收縮余量:由于鑄件在澆注后的冷卻收縮,制作模樣時要加上這部分收縮尺寸。
優點:
粘土的資源豐富、價格便宜。使用過的粘土濕砂經適當的砂處理后,絕大部分均可回收再用;
制造鑄型的周期短、工效高;
混好的型砂可使用的時間長;
適應性很廣。小件、大件,簡單件、復雜件,單件、大批量都可采用;
缺點及局限性:
因為每個砂質鑄型只能澆注一次,獲得鑄件后鑄型即損壞,必須重新造型,所以砂型鑄造的生產效率較低;
鑄型的剛度不高,鑄件的尺寸精度較差;
鑄件易于產生沖砂、夾砂、氣孔等缺陷。
2. 熔模鑄造
用蠟料做模樣時,熔模鑄造又稱"失蠟鑄造"。熔模鑄造通常是指在易熔材料制成模樣,在模樣表面包覆若干層耐火材料制成型殼,再將模樣熔化排出型殼,從而獲得無分型面的鑄型,經高溫焙燒后即可填砂澆注的鑄造方案。由于模樣廣泛采用蠟質材料來制造,故常將熔模鑄造稱為“失蠟鑄造”。
可用熔模鑄造法生產的合金種類有碳素鋼、合金鋼、耐熱合金、不銹鋼、精密合金、永磁合金、軸承合金、銅合金、鋁合金、鈦合金和球墨鑄鐵等。
圖片
熔模鑄造工藝過程
優點:
尺寸精度較高。一般可達CT4-6(砂型鑄造為CT10~13,壓鑄為CT5~7);
可以提高金屬材料的利用率。熔模鑄造能顯著減少產品的成形表面和配合表面的加工量,節省加工臺時和刃具材料的消耗;
能最大限度地提高毛坯與零件之間的相似程度,為零件的結構設計帶來很大方便。鑄造形狀復雜的鑄件熔模鑄造能鑄出形狀十分復雜的鑄件,也能鑄造壁厚為0.5mm、重量小至1g的鑄件,還可以鑄造組合的、整體的鑄件;
不受合金材料的限制。熔模鑄造法可以鑄造碳鋼、合金鋼、球墨鑄鐵、銅合金和鋁合金鑄件,還可以鑄造高溫合金、鎂合金、鈦合金以及貴金屬等材料的鑄件。對于難以鍛造、焊接和切削加工的合金材料,特別適宜于用精鑄方法鑄造;
生產靈活性高、適應性強熔模鑄造既適用于大批量生產,也適用小批量生產甚至單件生產。
缺點及局限性:
鑄件尺寸不能太大工藝過程復雜鑄件冷卻速度慢。熔模鑄造在所有毛坯成形方法中,工藝最復雜,鑄件成本也很高,但是如果產品選擇得當,零件設計合理,高昂的鑄造成本由于減少切削加工、裝配和節約金屬材料等方面而得到補償,則熔模鑄造具有良好的經濟性。
3. 壓鑄
壓鑄工藝原理是利用高壓將金屬液高速壓入一精密金屬模具型腔內,金屬液在壓力作用下冷卻凝固而形成鑄件。
圖片
壓力鑄造 a) 合型澆注 b) 壓射 c) 開型頂件
冷、熱室壓鑄是壓鑄工藝的兩種基本方式。冷室壓鑄中金屬液由手工或自動澆注裝置澆入壓室內,然后壓射沖頭前進,將金屬液壓入型腔。在熱室壓鑄工藝中,壓室垂直于坩堝內,金屬液通過壓室上的進料口自動流入壓室。壓射沖頭向下運動,推動金屬液通過鵝頸管進入型腔。金屬液凝固后,壓鑄模具打開,取出鑄件,完成一個壓鑄循環。
圖片
壓鑄工藝流程圖
優點:
產品質量好。鑄件尺寸精度高,一般相當于6~7級,甚至可達4級;表面光潔度好,一般相當于5~8級;強度和硬度較高,強度一般比砂型鑄造提高25~30%,但延伸率 降低約70%;尺寸穩定,互換性好;可壓鑄薄壁復雜的鑄件;
生產效率高。機器生產率高,例如國產JⅢ3型臥式冷空壓鑄機平均八小時可壓鑄600~700次,小型熱室壓鑄機平均每八小時可壓鑄3000~7000次;壓鑄型壽命長,一付壓鑄型,壓鑄鐘合金,壽命可達幾十萬次,甚至上百萬次;易實現機械化和自動化;
經濟效果優良。由于壓鑄件尺寸精確,表泛光潔等優點。一般不再進行機械加工而直接使用,或加工量很小,所以既提高了金屬利用率,又減少了大量的加工設備和工時;鑄件價格便易;可以采用組合壓鑄以其他金屬或非金屬材料。既節省裝配工時又節省金屬。
缺點及局限性:
壓鑄時由于液態金屬充填型腔速度高,流態不穩定,故采用一般壓鑄法,鑄件易產生氣孔,不能進行熱處理;
對內凹復雜的鑄件,壓鑄較為困難;
高熔點合金(如銅,黑色金屬),壓鑄型壽命較低;
不宜小批量生產,其主要原因是壓鑄型制造成本高,壓鑄機生產效率高,小批量生產不經濟。
4. 金屬型鑄造
又稱硬模鑄造,它是將液體金屬澆入金屬鑄型,以獲得鑄件的一種鑄造方法。鑄型是用金屬制成,可以反復使用多次(幾百次到幾千次),又叫永久型鑄造。
金屬型的結構
一般的,金屬型用鑄鐵和鑄鋼制成。鑄件的內腔既可用金屬芯、也可用砂芯。金屬型的結構有多種,如水平分型、重直分型及復合分型。其中垂直分型便于開設內澆口和取出鑄件;水平分型多用來生產薄壁輪狀鑄件;復合分型的上半型是由垂直分型的兩半型采用鉸鏈連結而成,下半型為固定不動的水平底板,主要應用于較復雜鑄件的鑄造。
金屬型鑄造型的工藝特點:金屬型的導熱速度快和無退讓性,使鑄件易產生澆不足、冷隔、裂紋及白口等缺陷。此外,金屬型反復經受灼熱金屬液的沖刷,會降低使用壽命,為此應采用以下輔助工藝措施。
預熱金屬型:澆注前預熱金屬型,可減緩鑄型的冷卻能力,有利于金屬液的充型及 鑄鐵的石墨化過程。生產鑄鐵件,金屬型預熱至250~350℃;生產有色金屬件預熱至100~250℃。
刷涂料:為保護金屬型和方便排氣,通常在金屬型表面噴刷耐火涂料層,以免金屬 型直接受金屬液沖蝕和熱作用。因為調整涂料層厚度可以改變鑄件各部分的冷卻速度,并有利于金屬型中的氣體排出。澆注不同的合金,應噴刷不同的涂料。如鑄造鋁合金件,應噴刷由氧化鋅粉、滑石粉和水玻璃制成的涂料;對灰鑄鐵件則應采用由石墨粉、滑石粉、耐火粘土粉及桃膠和水組成的涂料。
澆注:金屬型的導熱性強,因此采用金屬鑄型時,合金的澆注溫度應比采用砂型高 出20~30℃。一般的,鋁合金為680℃~740℃;鑄鐵為1300℃~1370℃;錫青銅為1100~1150℃。薄壁件取上限,厚壁件取下限。鑄鐵件的壁厚不小于15mm,以防白口組織。
開型:開型愈晚,鑄件在金屬型內收縮量愈大,取出采用困難,而且鑄件易產生大 的內應力和裂紋。通常鑄鐵件的出型溫度700~950℃,開型時間為澆注后10~60秒。
優點:
與砂型鑄造相比,金屬型鑄造有如下優點:
復用性好,可“一型多鑄”,節省了造型材料和造型工時。
由于金屬型對鑄件的冷卻能力強,使鑄件的組織致密、機械性能高。
鑄件的尺寸精度高,公差等級為IT12~IT14;表面粗糙度較低,Ra為6.3m。
金屬型鑄造不用砂或用砂少,改善了勞動條件。
缺點及局限性:
金屬型的制造成本高、周期長、工藝要求嚴格,不適用于單件小批量鑄件的生產,主要適用于有色合金鑄件的大批量生產,如飛機、汽車、內燃機、摩托車等用的鋁活塞、汽缸體、汽缸蓋、油泵殼體及銅合金的軸瓦、軸套等。對黑色合金鑄件,也只限于形狀較簡單的中、小鑄件。
5. 低壓鑄造
低壓鑄造是指使液體金屬在較低壓力(0.02~0.06MPa)作用下充填鑄型,并在壓力下結晶以形成鑄件的方法。
圖片
低壓鑄造工藝原理圖:1—保溫室 2—坩堝 3—升液管 4—貯氣罐 5—鑄型
低壓鑄造的工作原理下圖所示。把熔煉好的金屬液倒入保溫坩堝,裝上密封蓋,升液導管使金屬液與鑄型相通,鎖緊鑄型,緩慢地向坩堝爐內通入干燥的壓縮空氣,金屬液受氣體壓力的作用,由下而上沿著升液管和澆注系統充滿型腔,并在壓力下結晶,鑄件成型后撤去坩堝內的壓力,升液管內的金屬液降回到坩堝內金屬液面。開啟鑄型,取出鑄件。
圖片
低壓鑄造示意圖
優點:
澆注時金屬液的上升速度和結晶壓力可以調節,故可適用于各種不同鑄型(如金屬型、砂型等),鑄造各種合金及各種大小的鑄件;
采用底注式充型,金屬液充型平穩,無飛濺現象,可避免卷入氣體及對型壁和型芯的沖刷,鑄件的氣孔、夾渣等缺陷少,提高了鑄件的合格率;
鑄件在壓力下結晶,鑄件組織致密、輪廓清晰、表面光潔,力學性能較高,對于大薄壁件的鑄造尤為有利;
省去補縮冒口,金屬利用率提高到90%~98%;
勞動強度低,勞動條件好,設備簡易,易實現機械化和自動化。
缺點及局限性:
升液管壽命短,且在保溫過程中金屬液易氧化和產生夾渣。主要用來鑄造一些質量要求高的鋁合金和鎂合金鑄件,如氣缸體、缸蓋、曲軸箱和高速內燃機的鋁活塞等薄壁件。
6. 離心鑄造
離心鑄造是將金屬液澆入旋轉的鑄型中,在離心力作用下填充鑄型而凝固成形的一種鑄造方法。
離心鑄造的分類
根據鑄型旋轉軸線在空間的位置,常見的離心鑄造可分為兩種:
臥式離心鑄造:鑄型的旋轉軸線處于水平狀態或與水平線夾角很小(<4°)時的離心鑄造。
立式離心鑄造:鑄型的旋轉軸線處于垂直狀態時的離心鑄造稱為立式離心鑄造。
鑄型旋轉軸與水平線和垂直線都夾有較大角度的離心鑄造稱為傾斜軸離心鑄造,但應用很少。
圖片
a)立式離心鑄造 b)立式離心澆注成形鑄件 c)臥式離心鑄造
1,16—澆包 2,14—鑄型 3,13—液體金屬 4—帶輪和帶 5—旋轉軸 6—鑄件 7—電動機8—澆注系統 9—型腔 10—型芯 11—上型 12—下型 15—澆注槽 17—端蓋
優點:
用離心鑄造生產空心旋轉體鑄件時,可省去型芯、澆注系統和冒口;
由于旋轉時液體金屬在所產生的離心力作用下,密度大的金屬被推往外壁,而密度小的氣體、熔渣向自由表面移動,形成自外向內的定向凝固,因此補縮條件好,鑄件組織致密,力學性能好;
便于澆注“雙金屬”軸套和軸瓦,如在鋼套內鑲鑄一薄層銅襯套,可節省價格較貴的銅料;
充型能力好;
消除和減少澆注系統和冒口方面的消耗。
缺點及局限性:
鑄件內自由表面粗糙,尺寸誤差大,品質差;
不適用于密度偏析大的合金(如鉛青銅)及鋁、鎂等合金。
三、鑄造缺陷及其控制方法
鑄件缺陷種類繁多,產生缺陷的原因也十分復雜。它不僅與鑄型工藝有關,而且還與鑄造合金的性制、合金的熔煉、造型材料的性能等一系列因素有關。因此,分析鑄件缺陷產生的原因時,要從具體情況出發,根據缺陷的特征、位置、采用的工藝和所用型砂等因素,進行綜合分析,然后采取相應的技術措施,防止和消除缺陷。
1. 澆不到
鑄件局部有殘缺、常出現在薄壁部位、離澆道最遠部位或鑄件上部。殘缺的邊角圓滑光亮不粘砂。
產生原因:
澆注溫度低、澆注速度太慢或斷續澆注;
橫澆道、內澆道截面積小;
鐵水成分中碳、硅含量過低;
型砂中水分、煤粉含量過多,發氣量大,或含泥量太高,透氣性不良;
上砂型高度不夠,鐵水壓力不足。
防止方法:
提高澆注溫度、加快澆注速度,防止斷續澆注;
加大橫澆道和內澆道的截面積;
調整爐后配料,適當提高碳、硅含量;
鑄型中加強排氣,減少型砂中的煤粉,有機物加入量;
增加上砂箱高度。
2. 未澆滿
鑄件上部殘缺,直澆道中鐵水的水平面與鑄件的鐵水水平面相平,邊部略呈圓形。
產生原因:
澆包中鐵水量不夠;
澆道狹小,澆注速度又過快,當鐵水從澆口杯外溢時,操作者誤認為鑄型已經充滿,停澆過早。
防止方法:
正確估計澆包中的鐵水量;
對澆道狹小的鑄型,適當放慢澆注速度,保證鑄型充滿。
3. 損傷
鑄件損傷斷缺。
產生原因:
鑄件落砂過于劇烈,或在搬運過程中鑄件受到沖撞而損壞;
滾筒清理時,鑄件裝料不當,鑄件的薄弱部分在翻滾時被碰斷;
冒口、冒口頸截面尺寸過大;冒口頸沒有做出敲斷面( 凹槽)。或敲除澆冒口的方法不正確,使鑄件本體損傷缺肉。
防止方法:
鑄件在落砂清理和搬運時,注意避免各種形式的過度沖撞、振擊,避免不合理的丟放;
滾筒清理時嚴格按工藝規程和要求進行操作;
修改冒口和冒口頸尺寸,做出冒口頸敲斷面,正確掌握打澆冒口的方向。
4. 粘砂和表面粗糙
粘砂是一種鑄件表面缺陷,表現為鑄件表面粘附著難以清除的砂粒;如鑄件經清除砂粒后出現凹凸不平的不光滑表面,稱表面粗糙。
產生原因:
砂粒太粗、砂型緊實度不夠;
型砂中水分太高,使型砂不易緊實;
澆注速度太快、壓力過大、溫度過高;
型砂中煤粉太少;
模板烘溫過高,導致表面型砂干枯;或模板烘溫過低,型砂粘附在模板上。
防止方法:
在透氣性足夠的情況下,使用較細原砂,并適當提高型砂緊實度;
保證型砂中穩定的有效煤粉含量;
嚴格控制砂水分;
改進澆注系統,改進澆注操作、降低澆注溫度;
控制模板烘烤溫度,一般與型砂溫度相等或略高。
5. 砂眼
在鑄件內部或表面充塞有型砂的孔眼。
產生原因:
型砂表面強度不夠;
模樣上無圓角或拔模斜度小導致鉤砂、鑄型損壞后沒修理或沒修理好就合箱;
砂型在澆注前放置時間過長,風干后表面強度降低;
鑄型在合箱時或搬運過程中損壞;
合箱時型內浮砂未清除干凈,合箱后澆口杯沒蓋好,碎砂掉進鑄型。
防止方法:
提高型砂中粘士含量、及時補加新砂,提高型砂表面強度;
模樣光潔度要高,并合理做出拔模斜度和鑄造圓角。損壞的鑄型要修好后再合箱;
縮短澆注前砂型的放置時間;
合箱或搬運鑄型時要小心,避免損壞或掉入砂型腔砂粒;
合箱前清除型內浮砂,并蓋好澆口。
6. 披縫和脹砂
披縫常出現在鑄件分型面處,是垂直于鑄件表面,且厚薄不均勻的薄片狀金屬突起物。脹砂是鑄件內、外表面局部脹大,形成不規則的瘤狀金屬突起物。
產生原因:
緊實度不夠或不勻;
面砂強度不夠、或型砂水分過高;
液態金屬壓頭過大、澆注速度太快。
防止方法:
提高鑄型緊實度、避免局部過松;
調整混砂工藝、控制水分,提高型砂強度;
降低液態金屬的壓頭、降低澆注速度。
7. 抬箱
鑄件在分型面處有大面積的披縫,使鑄型外形尺寸發生變化。抬箱過大,造成跑火——鐵水自分型面外溢,嚴重時造成澆不足缺陷。
產生原因:
砂箱未緊固、壓鐵質量不夠或去除壓鐵過早;
澆注過快,沖擊力過大;
模板翅曲。
防止方法:
增加壓鐵重量,特鐵水凝固后再去除壓鐵;
降低澆包位置,降低澆注速度;
修正模板。
8. 掉砂
鑄件表面上出現的塊狀金屬突起物,其外形與掉落的砂塊很相似。在鑄件其它部位,則往往出現砂眼或殘缺。
產生原因:
模樣上有深而小的凹槽,同于結構特征或拔模斜度小,起模時將砂型帶壞或震裂;
緊實度不勻,鑄型局部強度不足;
合箱、搬運鑄型時,不小心使鑄型局部砂塊掉落。
防止方法:
模樣拔模斜度要合適、表面光潔;
鑄型緊實度高且均勻;
合箱、搬運過程中,操作小心。
9. 錯型(錯箱)
鑄件的一部分與另一部分在分型面的接縫處錯開,發生相對位移,使鑄件外形與圖紙不相符合。
產生原因:
模樣制作不良,上下模沒有對準或模樣變形;
砂箱或模板定位不準確,或定位銷松動;
擠壓造型機上零件磨損,例如正壓板下襯板、反壓板軸承的磨損等;
澆注時用的套箱變形,搬運、圍箱時不注意,使上下鑄型發生位移。
防止方法:
加強模板的檢查和修理;
經常檢查砂箱、模板的定位銷及銷孔、并合理地安裝;
檢查擠壓造型機的有關零件,及時調整,磨損大的要更換;
定期對套箱整形。脫箱后的鑄型在搬運時要小心。在面澆注的砂型,應該做一排砂型圍一排。
10. 灰口和麻點
鑄件斷口呈灰黑色或出現黑色小點,中心部位較多,邊部較少,金相觀察可見到片狀石墨。
產生原因:
鐵水化學成分不合要求,碳、硅含量過高;
爐前孕育的鉍加入澆包內過早或過遲,或是鉍量不足。
防止方法:
正確選擇化學成分,合理配料,使鐵水中碳、硅量在規定范圍內;
增加鉍的加入量并嚴格爐前孕育工藝。
11. 裂紋(熱裂、冷裂)
鑄件外部或內部有穿透或不穿透的裂紋。熱裂時帶有暗色或黑色的氧化表面斷口外形曲折。冷裂是較干凈的脆性裂紋,斷口較平,具有金屬光澤或輕微的氧化色澤。
產生原因:
鐵水中碳、硅含苞欲放量過低,含硫量過高;
澆注溫度過高;
冒口頸過大、過短,造成局部過熱嚴重,或重口太小,補縮不好;
鑄件在清理、運輸過程中,受沖擊過大。
防止方法:
控制鐵水化學成分在規定的范圍內;
降低澆注溫度;
合理設計冒口系統;
鑄件在清理、運輸過程中避免過度沖擊。
12. 氣孔
氣孔的孔壁光滑明亮,形狀有圓形、梨形和針狀,孔的尺寸有大有小,產生在鑄件表面或內部。鑄件內部的氣孔在敲碎后或機械加工時才能被發現。
產生原因:
小爐料潮濕、銹蝕嚴重或帶有油污,使鐵水含氣量太多、氧化嚴重;
出鐵孔、出鐵槽、爐襯、澆包襯未洪干;
澆注溫度較低,使氣體來不及上浮和逸出;
爐料中含鋁量較高,易造成氫氣孔;
砂型透氣性不好、型砂水分高、含煤粉或有機物較多,使澆注時產生大量氣體且不易排出。
防止方法:
爐料要妥善管理,表面要清潔;
爐缸、前爐、出鐵口、出鐵槽、澆包必須烘干;
提高澆注溫度;
不使用鋁量過高的廢鋼;
適當降低型砂的水分、控制煤粉加入量,扎通氣孔等。
13. 縮松、疏松
分散、細小的縮孔,帶有樹枝關結晶的稱縮松,比縮松更細小的稱疏松。常出現在熱世部位。
產生原因:
鐵水中碳、硅含量過低,收縮大;
澆注速度太快、澆注溫度過高,使得液態收縮大;
澆注系統、冒口設計不當,無法實現順序凝固;
冒口太小,補縮不充分。
防止方法:
控制鐵水的化學成分在規定范圍內;
降低澆注速度和澆注溫度;
改進澆冒口系統,利用順序凝固;
加大冒口體積,保證充分補縮。
14. 反白口
鑄件斷口內部出現白口組織,邊緣部分出現灰口。
產生原因:
碳、硅含量較高的鐵水,含氫量過高;
爐料中帶入的鉻等白口形成元素過多;
元素偏析嚴重;
防止方法:
控制化學成分、碳、硅含量不宜過高;
爐襯、包襯要烘干;型砂水分不宜過高;
加強爐料管理,減少帶入白口化元素。
四、汽車鑄造新技術和新方向
1. 砂成形技術的發展趨勢
潮模造型經過手工緊實→震擊+壓實緊實→高壓+微震緊實→氣沖緊實→靜壓緊實幾個發展階段。靜壓造型技術實質是“氣沖預緊實+壓實”。有以下優點:鑄型輪廓清晰,表面硬度高且均勻,起模斜度小,型板利用率高,工藝裝備磨損小,鑄型表面光潔度高,鑄型型廢率低。因此,是目前最新、最先進的造型工藝,并已成為當今的主流緊實工藝。
當前,國外比較有名的制造靜壓造型設備的廠家有德國的 KW公司、HWS公司和意大利薩威力公司。國內汽車鑄造廠家大都選用HWS公司或KW公司制造的設備,如一汽鑄造公司、東風汽車鑄造廠、上海圣德曼鑄造公司、華東泰克西、山西三聯、廣西玉柴、無錫柴油機廠等。
2. 近凈形技術發展趨勢
鑄造成形工藝
消失模鑄造也稱氣化模鑄造、實型鑄造、無型腔鑄造,被鑄造界譽之為“21世紀的鑄造新技術”、“鑄造的綠色工程”。該工藝的方法是采用無粘結劑干砂加抽真空技術。我國有一百多家企業用該工藝生產箱體類、管件閥體類、耐熱耐磨合金鋼類等三大類鑄件,總產量超過10萬t。今后,該工藝將大量采用快速制造技術和模擬仿真技術,以縮短生產準備周期,實現鑄件的快捷生產。
熔模精密鑄造成形型工藝
熔模精密鑄造工藝有水玻璃制殼工藝、復合制殼工藝、硅溶膠制殼工藝。汽車產品材料有碳素鋼、合金鋼、有色合金與球墨鑄鐵。國外有高合金鋼、超合金材料。熔煉設備國內采用普通、快速中頻爐;國外采用真空爐、翻轉爐、高頻爐技術。熔模精密鑄造技術成型工藝將來的發展趨勢是產品離商品越來越近,傳統的精鑄件只作為毛坯,已經不適應市場的快速應變;產品的復雜程度和質量檔次越來越高;研發手段越來越強,化協作開始顯現,CAD、CAM、CAE的應用成為產品開發主要技術。
3. 制芯技術的發展趨勢
目前,國內外汽車鑄造制芯有三種制芯工藝,在現代汽車鑄造中常并行采用的主要工藝 有熱芯盒制芯、殼芯制芯、冷芯盒制芯等,傳統的合脂或油砂制芯已被淘汰。
制芯工藝技術有以冷芯盒技術為主的發展趨勢。一汽鑄造公司、東風汽車鑄造廠、上海圣德曼鑄造公司、華東泰克西、山西國際鑄造公司等均采用冷芯盒制芯技術。
4. 鑄鐵熔煉技術的發展趨勢
目前,國內外鑄鐵熔煉技術有兩種主要方式:一是采用大型熱風除塵沖天爐與工頻保溫爐雙聯熔煉工藝;二是采用中頻感應電爐熔煉工藝技術。
美國因達公司和彼樂公司生產的中頻爐技術開始越來越受到重視,該技術日益成熟,其清潔、環保、節能、高效、安全的優勢突出,是今后發展的方向。一汽鑄造公司、東風汽公司采用因達公司和彼樂公司生產的中頻爐和保溫爐技術。已經開發與應用的球化劑、孕育劑、蠕化劑和其他各種添加劑產品,形成商品化、標準化、規格化、系列化。
5. 合金氣缸體、氣缸蓋壓鑄成形技術
鋁合金是汽車上應用最快和最廣的輕金屬,因為鋁合金本身的性能已經達到質量輕、強度高、耐腐蝕的要求。最初,鋁合金僅用于一些不受沖擊的部件。后來,通過強化合金元素,鋁合金的強度大大提高,由于質輕、散熱性好等特性,可以滿足發動機活塞、氣缸體、氣缸蓋在惡劣環境下工作的要求。鋁合金氣缸體、氣缸蓋壓鑄成形核心技術可以提高凈化、精練、細化、變質等材質質量控制,使得鋁鑄件質量達到一致性和穩定性。
隨著我國汽車業的發展,特別是家用轎車的快速增加和汽車部件出口的增大,汽車鋁鑄件將有很大的增長。鋁氣缸蓋成形工藝主要有兩種,一是以歐美為代表的重力鑄造成型工藝,上海皮爾博格、南京泰克西等公司,選用意大利法塔公司重力鑄造機生產鋁氣缸蓋。二是以日韓為代表的低壓鑄造成型工藝,東風日產發動機分公司鋁壓鑄車間、廣東肇慶鑄造公司、天津豐田鑄造公司,選用日本新東等公司低壓鑄造機生產鋁氣缸蓋。
6. 半固態壓鑄成型技術
半固態技術發源于美國,因此在美國這一技術已經基本成熟,處于全球領先地位,被稱之為21世紀最有前途的材料成形加工工藝。Alumax公司率先將該技術轉化為生產力,生產的鋁合金汽車制動總泵體毛坯尺寸接近零件尺寸,加工量占鑄件質量的13%,同樣的金屬型鑄件的加工余量則占鑄件質量的40%。20世紀80年代以來,歐洲等國在半固態應用方面作了大量研究和應用工作。
7. 鑄鐵材質的發展趨勢
薄壁高強度灰鑄鐵件技術
灰鑄鐵件在汽車上大量應用,由于該材料具有低的成本和良好的鑄造性能優勢。隨著汽車技術輕量化要求,灰鑄鐵的增長和發展將受到一定的影響,因此加強薄壁高強度氣缸體、氣缸蓋鑄件技術的開發與應用將是發展趨勢。
蠕墨鑄鐵技術
蠕墨鑄鐵具有球墨鑄鐵的強度,與灰鑄鐵相比又有類似的防振、導熱能力及鑄造性能,有好的塑性和耐熱疲勞性能,可以解決大馬力氣缸蓋的熱疲勞裂紋問題。蠕墨鑄鐵廣泛應用的巨大潛在市場是在汽車業,其主要產品則是發動機氣缸體和大功率柴油機氣缸蓋鑄件。隨著汽車輕量化和比功率(kW/排量)的提高,氣缸體和氣缸蓋的工作溫度越來越高,許多部位的工作溫度超過200 ℃,在此溫度下,鋁合金的強度大幅度下降,而蠕鐵則具有很大的優勢。
球墨鑄鐵技術
球墨鑄鐵由于其高強度、高韌性和低價格,所以在汽車市場上仍有很大發展。汽車鑄造業球鐵主要有4類產品技術工藝的發展趨勢。一是鑄態珠光體、高強度的載貨車和轎車曲軸,鑄態鐵素體、高伸長率的汽車排氣管和橋殼底盤類鑄件;二是保安類鑄件,鑄態生產轎車轉向節;三是耐熱球鐵件,高硅鉬、中硅鉬、高鎳球鐵,該材質生產的排氣管件;四是奧貝球鐵,主要用于生產曲軸等產品。除上述外,汽車鑄造廠已經生產出鑄態球鐵冷激凸輪軸。
8. 鑄造過程計算機應用技術發展趨勢
隨著汽車鑄造技術的快速發展,為縮短鑄件生產準備周期和降低新產品開發的風險,采用快速原型技術、計算機仿真模擬、三維建模、數控技術的應用越來越廣。快速原型技術應用開發新產品試制用的模樣及熔模鑄造的蠟模外,還可以制做酚醛樹脂殼型、殼芯,可以直接用來裝配成砂型。模擬造型過程正在成為國際汽車鑄造關注的前沿領域之一。應用Magma、華鑄軟件對新產品的鑄件充型、凝固的溫度場和流動場模擬分析處理,預測和分析鑄件的缺陷。
9. 鑄造檢測技術
無損檢測技術的應用越來越廣,對重要件時常采用熒光磁粉檢測表面裂紋;采用超聲波或音頻檢測球鐵的球化率;渦流檢測鑄件的基體組織(珠光體含量)。為滿足重要件檢測的要求,有的將上述三項檢測儀器組合成一條自動檢測線。
10. 綠色鑄造技術發展趨勢
“綠色鑄造”是使鑄造產品從設計、制造、包裝、運輸、使用到報廢處理整個產品生命周期中,對環境的負面影響最小,資源效率最高。鑄造行業歷來被認為是高能耗、高污染的行業,要不斷開發新的節能、清潔、低排放、低污染的鑄造材料以投入生產使用。